Blog
The Top 5 Reasons Dental Practices Don’t Own a Cassette-Based Instrument Management System
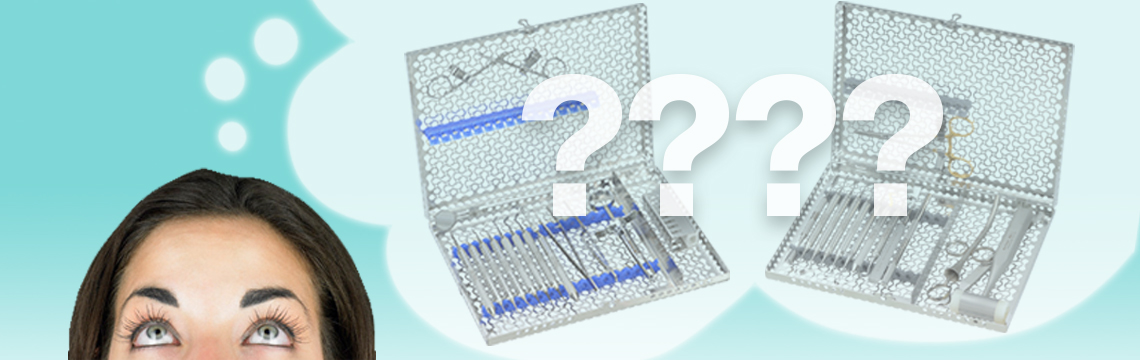
Dental professionals have a lot on their plates these days. There is a tremendous amount to think about, such as practice profitability, technology investments, team efficiency, new patient acquisition, and continuing education — just to name a few. With all of this to balance, it can be difficult to take a step back and look at specific processes that happen every day to determine if there are better, faster and safer ways to do things. Instrument reprocessing and sterilization is one of those areas and is a critical component to developing a best practice approach to dental infection control. Is there an optimal way to develop a path forward here? Click here to understand the potential ROI of implementing an IMS into your practice.
When exploring this question, it is instructive to look to the Centers for Disease Control and Prevention. The CDC indicates that dental practices should minimize exposure to potential contaminants by handling sharp instruments carefully. The best way to do that is by placing them in a container that will protect clinicians from injuries during transport and reprocessing.
OK, so is there any magic solution for this? Well, it might not be magic, but for practices who want to employ a contemporary method to instrument re-processing, a cassette-based instrument management system is a great place to start.
Unfortunately, many practices’ dental infection control is still based on carrying instruments with a tray and storing them in bundles, which increases the risk of sharps injuries and impairs the dental office workflow. A better way is to implement an instrument management system (IMS), which is designed to ensure that instruments are transported, processed and stored in cassettes, resulting in improved overall safety and optimized workflow.
“OSHA regulations require that sharp, contaminated instruments be transported in covered, puncture-resistant containers,” says Mary Govoni, a consultant who specializes in OSHA compliance. “Therefore, carrying instruments loose on a tray is an OSHA violation.
Even more important, is that the team needs to be protected from punctures or cuts to their hands while transporting, cleaning and preparing the instruments for sterilization.”
So, if many dental practices are not utilizing a cassette-based sterilization approach, the question is: why not? Let’s look at the most common reasons for not embracing the IMS solution — and why some of these reasons are ripe for myth-busting.
1. Unfamiliar with the system Often, dental professionals are hesitant to invest in an IMS because there isn’t full knowledge of how available the return on that investment is, or what an IMS really does. Think of it as an extra assistant: the system standardizes procedural set-ups and creates a process that is less people-dependent. And the fact is that an IMS saves time (approximately five to 10 minutes per procedure), protects instruments (ensuring you’re equipped with better, longer lasting instruments that don’t need to be replaced as often), protects the staff, reduces training time and optimizes the practice workflow, which allows more patients to be seen in a day. Having an IMS in use means fewer sharps injuries and less overtime pay given to staff members who are trying to catch up at the end of the day.
A consultation is key to understanding the needs of the practice and identifying where opportunities may exist. For instance, perhaps the practice is looking to add more patients without adding more hours. An IMS can help with that by saving time in the practice workflow.
2. There isn’t enough space
Once a practice starts using cassettes, it quickly becomes apparent how much space all of those pouches and trays required. Having an IMS actually saves on space because the instruments stay within the cassettes, eliminating the need to store the instruments and the tray separately. Here's how it works:
3. If it ain’t broke... Unfortunately, not having an IMS means practices may not be fully optimizing their time or maximizing the safety of patients and staff. There may also be a lack of awareness regarding the enhanced level of efficiency that can be gained in their dental sterilization process.
“In terms of efficiency, it takes more time to handle the instruments individually than it does to handle the instruments in an instrument cassette or some type of box or container,” says Govoni. “The cassette or container is only one thing to handle during transport, cleaning and sterilization — one per procedure, rather than many per procedure. In addition, instruments are protected during cleaning when in a cassette, which helps them last longer.”
If you’re not sure where your practice stands in regards to the CDC’s suggestions, head over to our site to take a self-assessment regarding your instrument processing and infection prevention protocols. You can also check out this video that demonstrates the differences in the IMS and manual processes, side by side.
And if you’re still not convinced, here is a video testimonial from dental professionals who are happy they made the switch to an IMS in their practice. Once the change is made, it is hard to imagine life without cassettes.
4. Bigger ticket investments are prioritized Every practice has a wish list: Whether it’s for newer technology or updated systems, certain things are at the top of that wish list, and unfortunately, smaller-in-scope products and solutions may not always be prioritized. In fact, many practices try to save on smaller ultrasonic baths or autoclaves.
However, increasing efficiency and optimizing the workflow is always a top priority, and having the right equipment to make reprocessing smoother and more effective allows the team to focus on more value-added activities.
The path towards better dental infection control can start by adding a three-gallon ultrasonic and a 10-inch chamber sterilizer. For more tips and best practices click here to identify any potential issues in the cleaning process and sign up for a sterilization observation consultation.
5. The cost is too high When considering the overall investment, it certainly seems that the few thousand dollars it takes to implement an IMS system certainly represents compelling value. Think about how much money is spent on replacing missing or broken instruments each year. Or, how much just one sharps injury costs the practice. To make it even easier to invest in an IMS upfront, Hu-Friedy offers offices a set-up rebate of 10 percent in cash or free goods. We also offer a rebate of 15 percent twice a year.
At the end of the day, having an IMS in the practice simplifies the workflow without sacrificing the strength of protocols, allowing the entire team to focus on the things that need their direct attention, like the patients. Dental professionals who implement cassettes into their practices don’t frame it as a cost. Instead, it is viewed as an investment that reduces risk and enhances productivity.
Click here to request a consultation from your local Hu-Friedy representative, and stay with us for the next blog topic on infection prevention products used in the sterilization area. We’ll cover why the products you use every day cannot be “every day” in quality.
FEATURED KEY OPINION LEADER
Read about Mary Govoni - Key Opinion Leader who is featured in this article.
Mary Govoni is a dental assistant and hygienist with over 40 years of experience in dentistry, including practice administration, clinical assisting and hygiene, dental assisting and hygiene education, consulting and seminar presentations. Her consulting and speaking areas of specialization include infection prevention and OSHA compliance, HIPAA compliance, ergonomics, and dental practice efficiency and team development.