Blog
Getting A Dirty Job Done. The Easy Way!
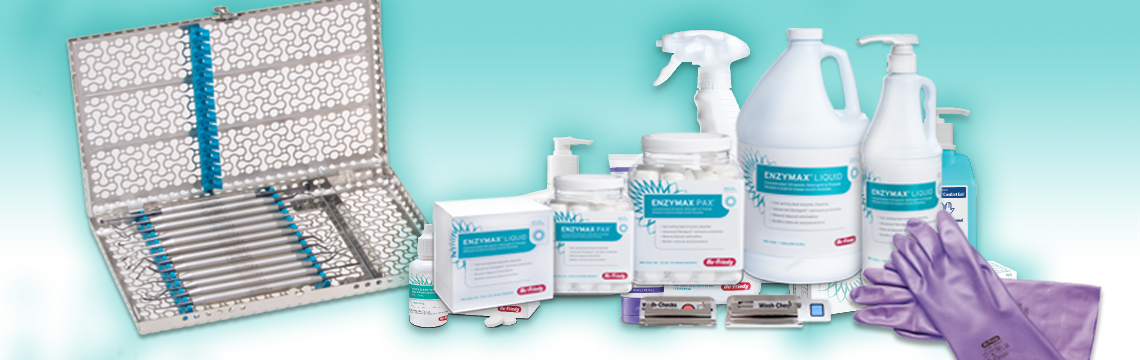
Quick tips to make your instrument processing thorough and safe
If you've ever watched the reality television show Dirty Jobs, you've probably concluded that dirty jobs are fun to watch or learn about, but not to do. However, these so-called "dirty jobs" play vital roles in society, keeping a world on the move going. When you think about it, especially on a microscopic level, instrument reprocessing is a dirty job, too, with countless microbes and organic debris being removed from the surfaces of instruments. However, instrument reprocessing plays a vital role in the dental practice and, without it, safe patient care would not be possible.
Fortunately, there are a range of developments and products in the dental market that make it possible for instrument reprocessing to be a clean job after all. With the right tools at your disposal, not only will you be confident that your instruments be clean and sterile, but you will stay safer and cleaner, too. What's more, these products will make your job easier.
First and foremost, you need to go into the instrument reprocessing area dressed for success. Used instruments are laden with microorganisms and biological debris like blood and saliva, which means you need to handle them the way you would a patient. Be sure you are wearing the appropriate PPE, including protective eyewear, face mask, impermeable smock, and gloves. However, we're not talking about standard exam gloves; in order to make this dirty job clean, you must wear chemical- and puncture-resistant utility gloves whenever handling contaminated instruments or performing instrument cleaning and decontamination procedures. The instrument reprocessing area poses a high risk of biohazardous sharps injuries – unless, of course, you have the appropriate protection.
One of the best investments your practice can make is a cassette-based instrument management system. A cassette-based system will organize your instruments from cleaning and sterilization through use and back again. Because your instruments all have their own "home" and are kept together, you reduce the risk of losing or misplacing instruments, making inventory and procedure preparation much easier. Additionally, the cassettes protect instruments during cleaning, packaging, sterilization, and transport, minimizing the risk of damage. Cassettes ensure that instruments are properly spaced apart and secured, increasing your confidence in the cleaning and sterilization process. Most importantly, cassettes reduce instrument handling to a minimum, reducing the chance of sharps injuries, protecting staff. You can save an average of five to ten minutes per procedure, thanks to the organization and efficiency these systems bring.
Cleaning can be a real chore, but it doesn’t need to be. Washing our clothes in the washtub with a washboard and lye went out of style a long time ago, replaced with automatic washing machines. Why should cleaning dental instruments be any different? The safer (and more efficient) option to manual hand scrubbing is to use an ultrasonic cleaner or an automated instrument washer (only one designed for dental instruments – please no dishwashers!). Ultrasonic baths function best when used with dual enzymatic cleaners. Look for ones specifically designed for dental instruments which contain both Protease enzymes (to break down proteins like blood and saliva) and Amylase enzymes (to break down carbohydrates and starches) to ensure the cleanest results. Additionally, your cleaning solutions should be formulated to protect your instruments. You wouldn’t use a bar of soap to wash your hair – you’d use shampoo and conditioner, and you’d likely go an extra step and choose a shampoo that is best for your hair type and needs (curly, dry, dyed, thin, etc.). Likewise, be sure your cleaning solutions will protect your instruments from the minerals naturally found in water and which cause buildup, spotting, and corrosion. Chelating agents and additives such as Steelguard™ agents will keep your instruments looking like new and working at their best.
Those of us who like to cook (or those who have ever had to care for children) know that cleaning up as you go along makes a big difference, maintaining order and organization – not to mention your own sanity. However, in a busy dental practice, it’s not always possible to put your cassette through a wash cycle the moment your patient leaves the chair. Moreover, it can be more efficient to process full loads of instruments. Using an enzymatic pre-cleaner, such as Enzymax spray-on gel or a pre-soaking bath can not only prevent this organic matter from drying, but will also begin to break it down making it easier to clean when it’s convenient for the staff or you have reached a full load. And always remember to thoroughly wipe off restorative composites and cement chairside with an alcohol gauze, immediately after placement, to prevent these durable materials from permanently affixing to the instrument.
Regardless of what it is that we are cleaning, we always want to be sure it is truly clean when we’re done. We wouldn’t want to eat with a fork that still had bits of last night’s dinner on it. Likewise, you never want to use dental instruments that haven’t been completely cleaned. ‘Ick factor’ aside, instruments that are not fully cleaned present a health hazard to patients. If an instrument is put into a sterilizer with any amount of debris on it, it will never be truly sterile. That is because the organic matter on it will serve as a shield, preventing heat, steam, or ethylene gas from ever reaching the microbes laying between it and the instrument’s surface. Put simply, a partially cleaned instrument is an unsterile – and unsafe – instrument.
Marie T. Fluent, DDS, is a respected authority on instrument processing. She provides a memorable analogy to illustrate the importance of completely clean instruments: “One of my favorite movies is The Princess Bride – a fairy tale adventure about a young woman and her one true love, Westley. In the film, Westley is pronounced ‘mostly dead’ when the obvious is stated: ‘Mostly dead is slightly alive!’ As I think of this quote, I can imagine inadequately cleaned dental instruments emerging from the autoclave. Germs on these instruments are indeed mostly dead, and unfortunately slightly alive – therefore, the instruments are not safe for patient care! However, if debris is thoroughly removed through the cleaning process, the sterilant can assuredly reach all surfaces of the instruments and germs will then be ‘completely dead’. Only then will instruments be sterile and safe for use on the next patient.”
To verify your cleaning, use cleaning monitors to ensure your instruments have been cleaned properly. Cleaning Monitors are single-use strips for your instrument washer or ultrasonic bath with an indicator that simulates biological debris found on instrumentation. If the instruments have been thoroughly washed, the indicator will disappear completely, allowing you to dry and later sterilize your instruments with confidence. Cleaning Monitors are one way to ensure instrument processing is never a dirty job.
There are many components to thorough and complete instrument processing. Dr. Fluent sums up the requirements: “To achieve ‘completely dead’ germs and provide sterile instruments for safe patient care, dental personnel who process instruments should have policies and procedures in place, be properly trained, equipped with proper PPE and supplies, and have manufacturer’s instructions readily available. Instrument processing requires multiple steps using specialized equipment; however, cleaning should always be the first step!”
At first glance, instrument processing may seem like a "dirty job", especially when the instruments are first transported from the operatory to the processing area. However, by using the latest advancements in instrument processing, you can rest assured this vital task will be a "clean job."
FEATURED KEY OPINION LEADER
Read about Marie T. Fluent, DDS - Key Opinion Leader. Dr. Marie Fluent is a graduate of the University of Michigan School of Dentistry and has enjoyed 25 years of clinical practice as a general dentist in Maryland, Virginia, and Michigan. She has served the dental profession as an assistant, administrator, dentist, educator, and infection prevention consultant. She has written numerous articles and has lectured extensively on infection control in the dental setting. Marie is currently an educational consultant for The Organization for Safety, Asepsis, and Prevention (OSAP).