Blog
Become a Lean Practice: How Instrument Management Can Improve Safety, Quality, Efficiency, and Profitability
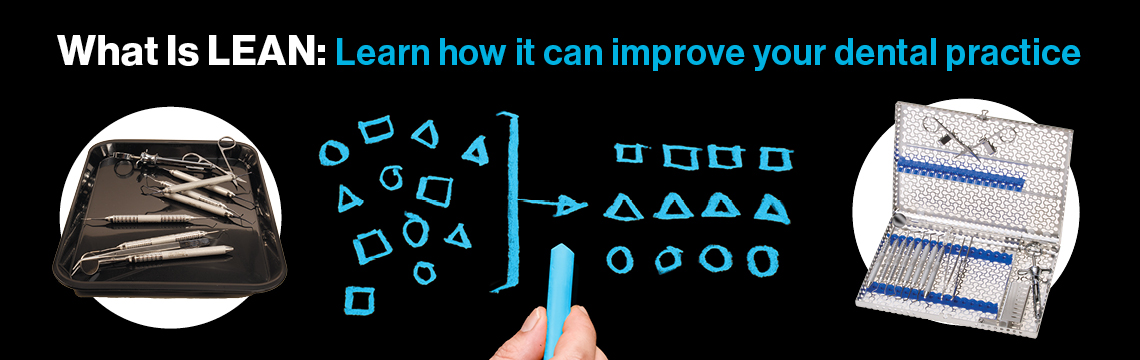
Improve Your Dental Practice with Lean
In some industries, the principles of Lean have been part of the landscape for a long time. But the concept of Lean can also be applied to your dental practice to improve safety, quality, efficiency, and profitability.
What exactly is Lean? Lean is an approach that uses metrics and problem-solving to reduce defects in production and resolve issues. The Lean method is focused primarily on eliminating waste in all forms, which includes defects, overproduction, waiting, non-utilized talent, transportation, inventory, motion, and extra processing.
There are plenty of benefits to applying Lean culture in dental practices.
It Can Increase Employee Engagement
Integral to Lean culture is the need for all employees to understand the organization’s or practice’s vision so they can contribute to that vision. In turn, leaders demonstrate respect for employees and reward them for their work.
This cyclical relationship helps improve employee morale and retention, ensures your entire staff is working at their best, increases overall productivity, and reduces patient and staff risk. In other words, Lean culture fosters an engaged workforce.
When you consider the current state of recruitment and retention in the dental practice space, being able to create a workplace where your staff loves working and encourages their colleagues to join them is ideal.
When employees understand the vision, they’re happier. They believe in what they’re doing and can imagine their role in the strategy. Keeping your people happy keeps your retention high.
It Can Empower Problem Solving
In hierarchical dental practices, the practice leader makes all the decisions, and staff follows through on them. But is that truly efficient in today’s work environment?
Of course, there are practice decisions that should be made only by dentists and owners. However, there is value in empowering your staff to make operational decisions that keep your office running and patients cared for, even when you aren’t in the office.
In Lean organizations, we think of problems as opportunities and are excited to solve issues so that we never repeat mistakes. So if everybody is always thinking about problems and solutions and all your defects going away and all your safety issues going away, you have continuous improvement.
You can do this by providing the information your team needs to make decisions. Spend time as a team brainstorming how to reorganize the office so you have fewer issues. Examine your practice's processes and ask the team to weigh in on improvements. In this way, everyone in the office becomes a problem solver and contributes to continuous improvement.
It Can Improve Patient Care
Getting the entire team involved in problem-solving doesn’t only result in better solutions and better efficiency, it results in better patient care — and higher job satisfaction. When your team is empowered to identify problems and develop solutions, your team makes fewer errors, and the impact on quality patient care and patient safety is significant. Your staff delivers high-quality care in shorter visits, and patient waiting time is reduced, all while patient outcomes improve.
The errors are reduced, and the time to service somebody is reduced. Safety, quality, and delivery are improved. You get more information in a faster and easier way. It’s big.
That means better patient satisfaction scores, more positive word-of-mouth promotion, and potentially more revenue.
It Can Reduce Waste
When thinking about Lean culture, waste reduction is really the entire point of the exercise. In the dental practice, this can translate to multiple areas such as:
Training
Think about the amount of retraining you do each time a new employee joins the team. If you retain more of your staff, you’ll spend less time going through the same training over and over. An even more important example is the institutional knowledge you’ve got in some of your long-term employees. When you allow staff to work together to problem-solve, your team learns from those legacy employees.
Another aspect of training is making sure it promotes consistency. A Lean-friendly approach is to create standardized processes that all employees follow so there’s no wasted time correcting mistakes and unlearning incorrect processes.
Office Workflow
One of the biggest advantages of Lean culture and examples of reduced waste pertains to the flow in your office. Again, think about how much time your staff spends walking around the practice, preparing for a patient visit, sterilizing instruments, pulling instrument packs for each procedure, looking for additional instruments, etc. There’s an opportunity to cut down on the wasted time that is dedicated to office flow.
Waste in these two areas, for instance, can be solved with consistency and processes, and both can be facilitated with instrument management.
Benefits of Instrument Management
Instrument management lends itself to standardization. When you standardize your procedures into an instrument management system (such as IMS™ Cassettes), you standardize single-piece flow in the office and during patient visits. When the IMS™ Cassettes are configured according to the procedure, it keeps instruments secure throughout the entire cycle, from patient use to presoak to cleaning and all the way through to reprocessing.
IMS™ Cassettes also reduce the amount of handling of contaminated instruments. Instead of keeping instruments loose for presoaking and cleaning, dental professionals should organize and store them in a cassette, which creates an optimal environment for reprocessing, protects instruments, and significantly reduces the risk of injuries.
It gives you improved efficiency because you have the right tool that you need at the right place. It encourages visual control because when you look at the IMS and there's an item missing, you can quickly see that it's missing, right? That improves safety, which automatically improves employee satisfaction.
Using IMS™ Cassettes can contribute to achieving Lean culture in many ways:
- Efficiency — Eliminate time-consuming steps to streamline reprocessing, which can save an hour or more each day.
- Safety & Compliance — Minimize how often contaminated instruments are handled, improving compliance during transportation and reprocessing while also reducing the risk of a costly sharps injury.
- Organization — Better organizes reprocessing flow, freeing up to seven linear feet of counter space, which can maximize space in sterilization areas. When coupled with the use of organizational tubs for procedural disposables, efficiency and organization are greatly improved as procedure needs are easily identified for quick patient setup.
- Instrument Protection — With high-quality medical-grade silicone rails, IMS™ Cassettes protect the integrity of instruments by keeping them in place and spaced out to create an optimal environment for proper reprocessing.
- Standardization — Create a system for managing procedural setups. Each setup includes all the instruments that are needed to help with onboarding and standardizing care throughout a single facility and even across multiple locations.
- Return on Investment — Make an immediate impact on a practice’s bottom line with the time saved, allowing them to see new patients and bring in tens of thousands of dollars in new revenue. Additionally, because they’re made of durable electropolished stainless steel, IMS™ Cassettes resist corrosion and discoloration, resulting in a longer life.
Implementing an instrument management system can have such an impact on most, if not all, of the factors that lead to Lean culture. This includes improved organization, compliance, efficiency, and safety in the practice.
To benefit from the principles of Lean in your dental practice, the key is to bring everybody to the table – and to never be completely satisfied. By freeing up time and streamlining processes, you can increase productivity and the overall patient experience.
Want to get started on streamlining your instrument reprocessing? Click here